Product
HEAT RECYCLING FOR INDUSTRY
TECHNOLOGY
Conventional heat pumps physically use the two-phase Rankine process. The superior Joule process or Brayton process has many advantages over this, e.g. in that it is single-phase (the working fluid always remains gaseous). However, the practical implementation was not considered feasible, as this process requires extremely high efficiency in compression. ecop has succeeded in achieving this efficiency of over 99% by having the entire process use centrifugal force and rotate – hence “Rotation Heat Pump”. The technology is protected by 68 patents from 6 patent families.
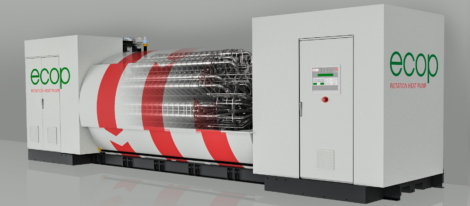
ENVIRONMENTAL PROTECTION
BENEFITS
For our customers – industrial companies and manufacturers of heat – the unique design results in a number of benefits:
- Production of heat sustainably and without dependence on fossil fuels
- Contribution to climate targets and decarbonisation
- Efficient use of waste heat
- Saving costs
Advantages
Due to its special design, the Rotation Heat Pump has a number of advantages over other technologies, which makes it highly attractive:

Conventional heat pump | Rotation Heat Pump | |
Efficiency / COP (dependent on the exact integration) | 2,5 – 5,0 | 4,0 – 7,0 |
Temperature range, sink (output) | 0°C to +80°C | 0°C to +200°C |
Maximum temperature rise | 60K | 100K |
Flexible temperature range with one machine | no | yes |
Significant source cooling possible | no | yes |
Summer and winter operation | no | yes |
Tools | Often harmful to the environment / toxic / flammable | environmentally friendly, non-toxic, incombustible inert gas |
Maintenance advantage | medium | high |
Installation advantage | low | high |
Purchase costs and integration effort | medium | medium |
Implementation
The ecop process is a thermodynamic cycle process.
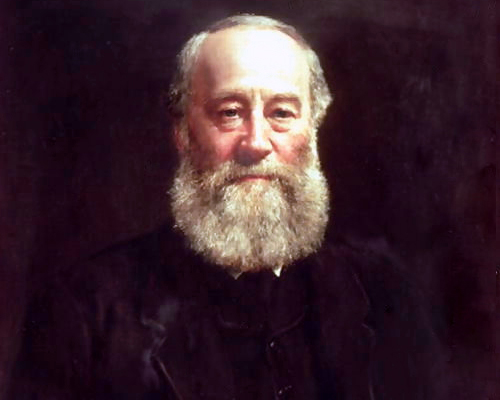
James Prescott Joule, Source Wikipedia
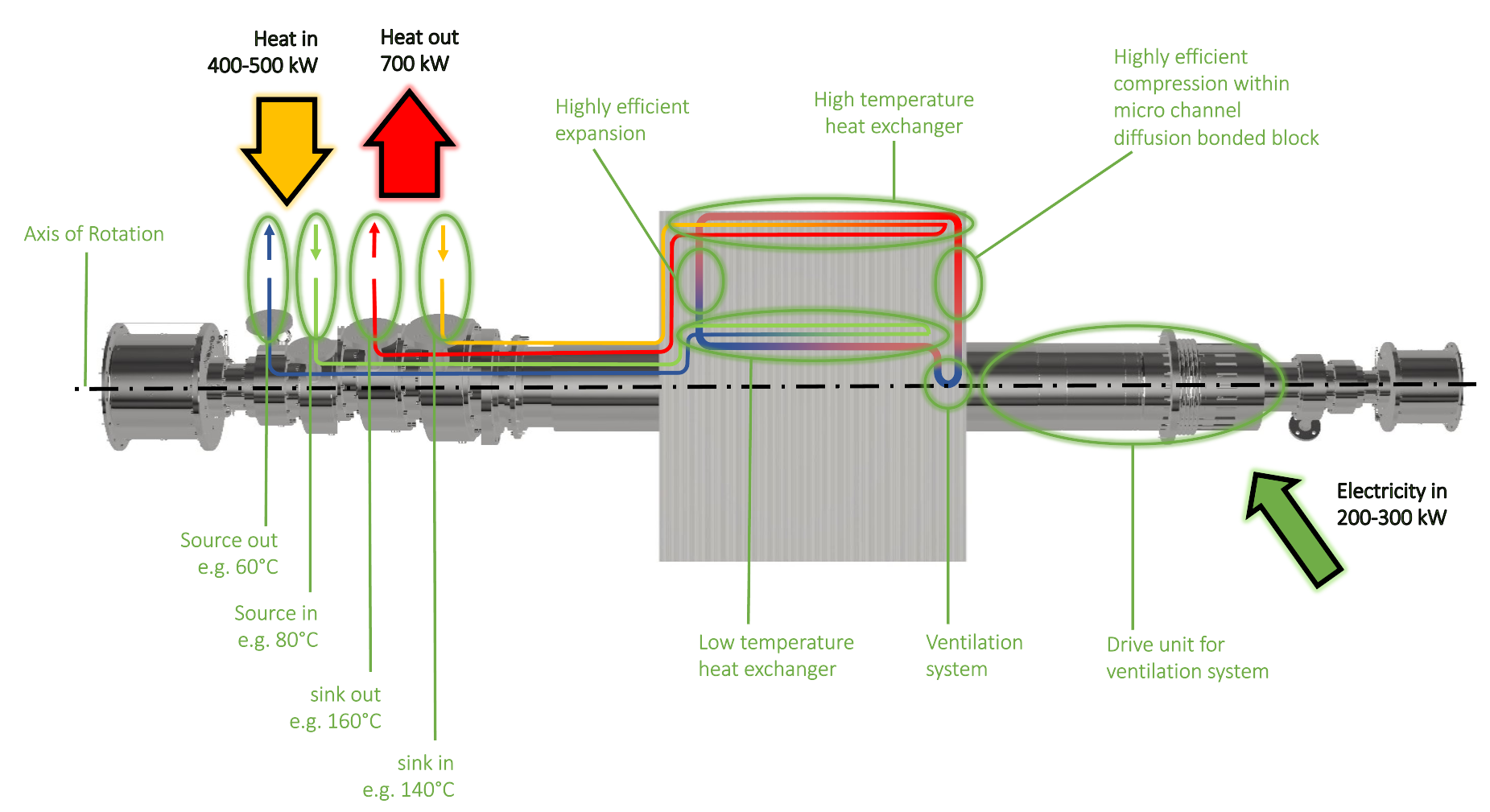
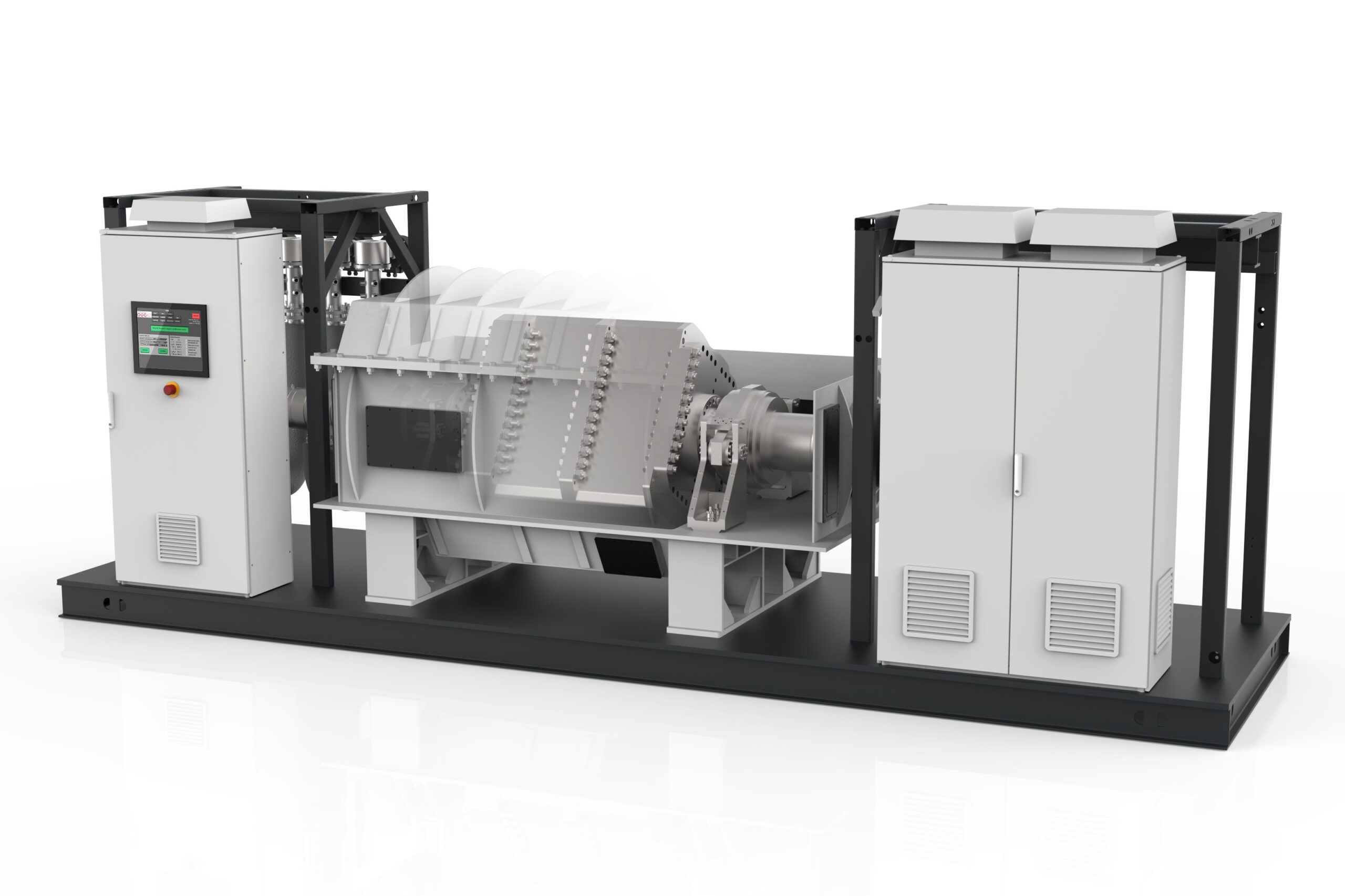
Variation of rotation speed for maximum efficiency.
Depending on the speed of rotation, there is a different pressure ratio between the outer and inner zone. That way, the compression and expansion pressure ratio can be changed. This results in a freely definable temperature difference between the low-pressure side (source) and high-pressure side (sink), which can be regulated via the rotational speed. Through the rotational speed of the fan, the flow rate and hence the transferrable heating capacity are regulated independently of the temperature increase. Hence, this technology facilitates maximum flexibility.
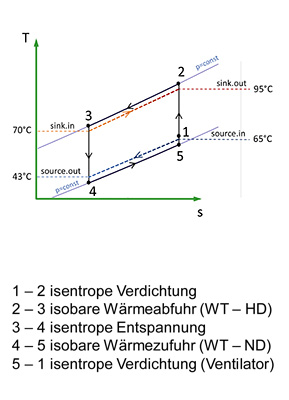
Modular rotor design: Optimum performance scaling
By combining several modules, the performance of the Rotation Heat Pump can be multiplied. With the help of diffusion bonding technology, rotor modules (so-called “cores”) with an output of 700 kW are created. However, around 50% of the requirements for industrial heat pumps are in the range up to 10 MW. Other suppliers address this by building larger systems. These need more space, are difficult to transport and implement and entail more risk in the event of a failure.
ecop’s technology allows several of the cores to be combined instead. For example, 8 cores can be combined in one machine. This increases the output to 5.6 MW. This leads to economies of scale in production and numerous benefits for our customers: Simple adjustment of the output, fast change of assembly groups, very good part load behaviour, a very small size, and quick set-up at customer site.
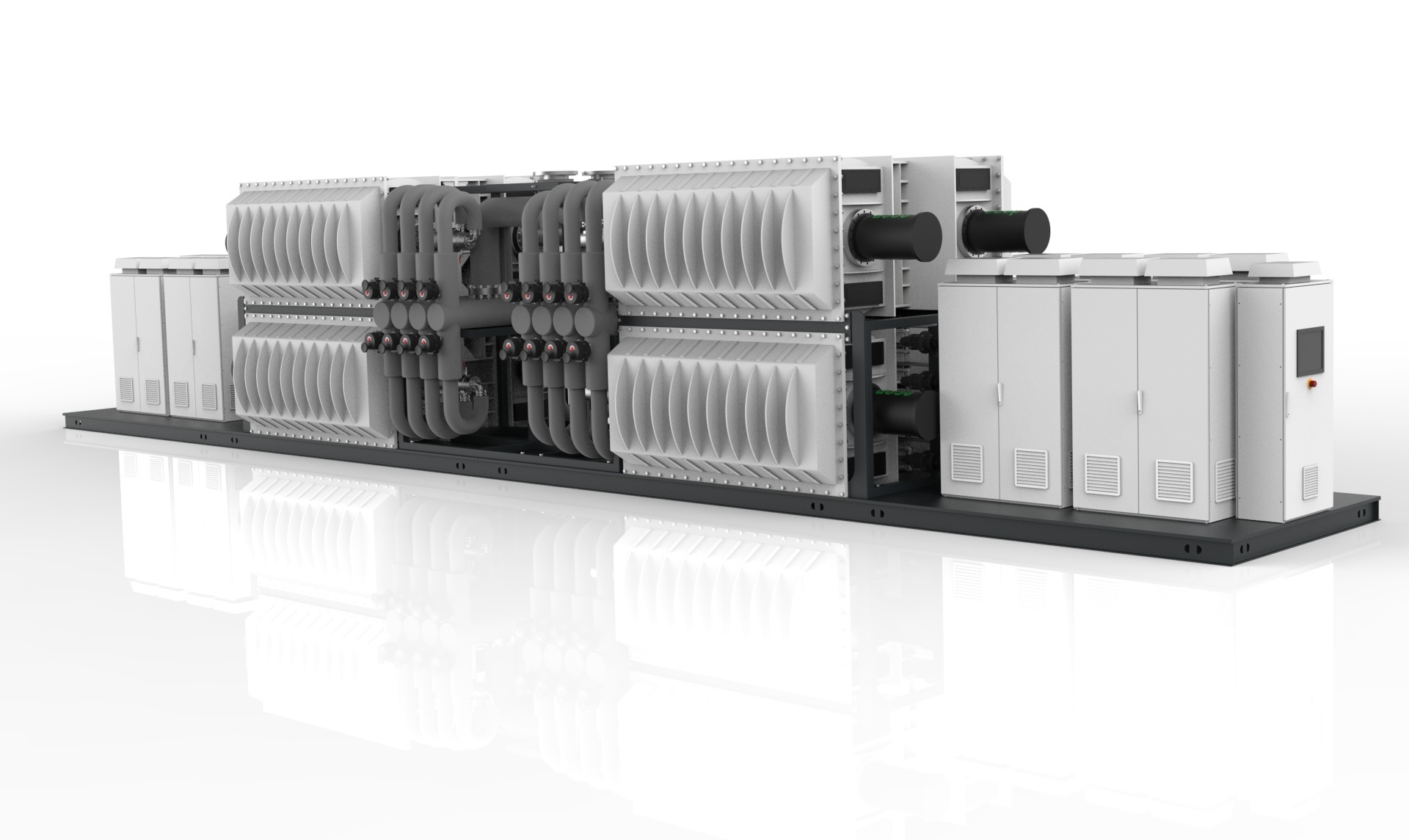
Articles
- Heat pump for different temperature levels – R+T Textilservice Issue 7-8 2024 (Source: Holzmann Medien GmbH & Co,KG)
- Ruler of 300 billion euros visits one of the funded projects – EU Regional Commissioner Elisa Ferreira to visit the heat pump developer Ecop – OÖ Nachrichten from 20.10.2022
- Wirtschaftswoche (2022)
- energy innovation austria – März 2022
ROHAN – DigitalTwin zur regelungstechnischen Optimierung einer Rotationswärmepumpe (S. 8f)
Quelle: www.energy-innovation-austria.at - Fernwärmetage 2022 – März 2022
Präsentation ecop Technologies GmbH - pv magazine Deutschland – März 2022
Leistungsstarke Rotationswärmepumpe für industrielle Anwendungen aus Österreich - Holzkurier – Februar 2022
Abwärme effizient nutzen
Archive
- Deutsche Kälte‐ und Klimatagung 2021 – November 2021
Präsentation ecop Technologies GmbH
Paper - Community Research and Development Information Service (CORDIS) from the European Commission – September 2021
CORDIS Artikel - Annex 58 – High-Temperature Heat Pumps – Juli 2021
Präsentation - 4th IIR-Gustav Lorentzen Conference on Natural Refrigerants – GL2020 – Dezember 2020
Paper - Deutsche Kälte‐ und Klimatagung 2020 – November 2020
Präsentation - 13th International Energy Agency Heat Pump Conference – Mai 2020
Paper - Deutsche Kälte‐ und Klimatagung 2019 – November 2019
Präsentation - 25. IIR International Congress of Refrigeration – August 2019
Präsentation ecop Technologies GmbH
Paper - Austromatisierung – Ausgabe Mai 2019
Rotierende Effizienz - flow der Verbund-Blog – Ausgabe Mai 2019
VERENA-Award: Rasante Wärmenutzung bei 1.800 Touren - Industriemagazin – Ausgabe Mai 2019
Revolutionär: Wärmepumpe für Großbetriebe - 14. FGW Fernwärmetage 2019 – März 2019
Präsentation - KKA Kälte Klima Aktuell – Ausgabe Großkälte 2018
Industrieller Einsatz einer Rotationswärmepumpe - FORUM Gas, Wasser, Wärme – Ausgabe 1/2018, Februar 2018
Forum Gas, Wärme, Wasser – Ausgabe 1_2018 - 12. Heat Pump Conference Rotterdam, Mai 2017
Präsentation ecop Technologies GmbH und Paper - 12. CADFEM ANSYS SIMULATION CONFERENCE AUSTRIA – Die Fachkonferenz zur Numerischen Simulation in der Produktentwicklung, April 2017
Präsentation „Simulationen der ecop ROTATION HEAT PUMP“ - Holzkurier – 08/17, Februar 2017 „Rotierende Wärmepumpe“, Seite 22 Verlagsseite
- 2. Praxis- und Wissensforum Fernwärme & Fernkälte, November 2016
Präsentation „Die ecop Rotationswärmepumpe für Fernwärmeanwendungen“ - Umweltschutz der Wirtschaft Spezial Industrie – No S/16 „Rotierende Wärmepumpe: Recycling auf die Spitze getrieben“, Seite 35 – 36
- Highlights der Energieforschung 2016 – Die Rolle der Wärmepumpe im zukünftigen Energiesystem
Vortrag & Video von Bernhard Adler - Konferenz EnergieInnovation Graz, März 2016
ecop Rotationswärmepumpe auf Basis eines Joule Prozesses - FFG Forschungserfolg – 2016
Wärmepumpen einmal anders - BBR – Leitungsbau, Brunnenbau, Geothermie – 07/08 2015 „Erweiterung der Fernwärmekapazität von Tiefengeothermie durch innovative Edelgas-Industriewärmepumpen“, Seite 58 – 63
- Euro Heat & Power – Juni 2015 „Innovative Wärmepumpe erzeugt bis -100°C Kälte und bis 200°C Wärme“, Seite 28 – 33
- VDI Forum: Wärmepumpenhebel/Großwärmepumpen – Projekte, Erfahrungen und Perspektiven – April 2015
Vortrag ecop Rotationswämepumpe von Bernhard Adler - CITplus – Das Praxismagazin für Verfahrens- und Chemieingenieure – März 2015
„Wenn sich das Gas im Kreise dreht – Kälteerzeugung und Wärmerecycling im Einklang mit der F-Gase Verordnung„, Seite 41-43 - Heat Pump Conference Montreal Mai 2014
Heat Pump for Process Industry - Wochenblatt für Papierfabrikation – Januar 2014 „Wärmerecycling durch Industriewärmepumpen“, Seite 18 – 21
- Process – Chemie, Pharma, Verfahrenstechnik – März 2013 „Mit weniger Energie mehr Wärme – Hochtemperaturwärmepumpe für den Einsatz in der Prozesstechnik“, Seite 78 -79
- Internationale Wärmepumpen-Konferenz Juli 2011 Tokio / Japan
Centrifugal Compression Turbo Heat Pump Made by ecop